Sputtering and evaporation
Lauren McCabe
Assistant DirectorBuilding: Becton Engineering and Applied Science Center, 5th floor
About the instruments
Physical vapor deposition (PVD) is a technique for synthesizing thin films by vaporizing target solids with high energy, which then condense onto substrate materials to form a thin layer. The most commonly employed PVD methods include electron-beam evaporation, thermal evaporation, and plasma sputtering. Our cleanroom features various tools utilizing these techniques. Please note that the compatibility of materials varies with each system, so consulting with a staff member before introducing new substrates is essential. Additionally, understanding the thermal tolerance of your substrate is crucial.
Available to Yale researchers & external researchers
Equipment list
- Denton Infinity 22 E-Beam Evaporator
- PVD E-Beam Evaporator-1
- PVD E-Beam Evaporator-2
- Nano38 Thermal Evaporator
- Kurt J. Lesker CMS-18 Sputtering System
- Kurt J. Lesker PVD 75 Indium Evaporator
Denton Infinity 22 E-Beam Evaporator
The Denton Infinity 22 is an electron beam evaporator used to deposit thin films of metals and dielectrics. It includes a 4-pocket electron gun for sequential in-situ deposition and a quartz crystal monitor for thickness control. The system achieves a base pressure of 10⁻⁶ to 10⁻⁷ Torr with an 8" cryopump.

- Available materials: Ag, Al, Al₂O₃, Au, Cr, Cu, Ge, HfO₂, Mo, MoO₃, Ni, Pd, Pt, Si, SiO₂, Ti, TiO₂, W
- Maximum sample size: 6"
- Substrate heating: Not available
- Base vacuum pressure: 10⁻⁶ to 10⁻⁷ Torr
- Tool manager: Lauren McCabe
- Location: Main Campus Cleanroom
- Internal rate: Included with cleanroom access
PVD E-Beam Evaporator-1
his ultra-high vacuum e-beam evaporator includes a 6-pocket source and supports ion beam assisted deposition (IBAD). It offers dual sample stages, automated control systems, and achieves base pressures down to 10⁻⁹ Torr. No substrate heating is available, but stages support chiller cooling and rotation.

- Available materials: Ti, Al, Nb, Au, Cu, Pt
- Maximum sample size: 6"
- Substrate heating: Not available
- Base vacuum pressure: ~10⁻⁹ Torr
- Tool manager: Lauren McCabe
- Location: Main Campus Cleanroom
- Internal rate: Included with cleanroom access
PVD E-Beam Evaporator-2
This e-beam evaporator provides ultra-pure film deposition under UHV conditions (~10⁻⁹ Torr) using a load-locked chamber and cryopump. The system supports six material pockets and features in-situ substrate heating up to 500°C, as well as tilting and rotation stages. Unique capabilities include annealing without vacuum break and in-situ cleaning using Ar, O₂, and H₂.
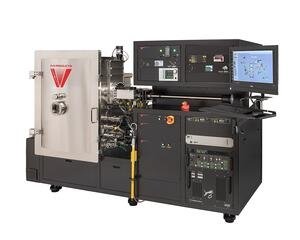
- Available materials: Au, Ag, Al, Cr, Cu, Nb, Ni, Pt, Ti
- Maximum sample size: 6"
- Substrate heating: Up to 500°C
- Base vacuum pressure: ~10⁻⁹ Torr
- Tool manager: Lauren McCabe
- Location: West Campus Cleanroom
- Internal rate: Included with cleanroom access
Nano38 Thermal Evaporator
The Kurt Lesker Nano38 uses resistive heating to thermally evaporate metals like Cr and Au at low rates. This compact system is ideal for creating thin metal layers, such as etch masks or contact pads.

- Available materials: Au, Cr
- Maximum sample size: 6"
- Substrate heating: Not available
- Base vacuum pressure: ~10⁻⁷ Torr
- Tool manager: Lauren McCabe
- Location: Main Campus Cleanroom
- Internal rate: Included with cleanroom access
Kurt J. Lesker CMS-18 Sputtering System
The CMS-18 is a magnetron sputtering system designed for UHV deposition of refractory metals. It supports Nb, Ta, and Re with a rotation stage capable of heating substrates up to 900°C. The base pressure reaches as low as 10⁻¹⁰ Torr.

- Available materials: Nb, Ta, Re
- Maximum sample size: 4"
- Substrate heating: Up to 900°C
- Base vacuum pressure: ~10⁻¹⁰ Torr
- Tool manager: Lauren McCabe
- Location: Main Campus Cleanroom
- Internal rate: Included with cleanroom access
Kurt J. Lesker PVD 75 Indium Evaporator
The Kurt J. Lesker Company® PRO Line PVD 75 is a high-vacuum thin film deposition system utilizing thermal evaporation. The system includes a dedicated 15 cc pocket for indium deposition only. Film thickness and growth rate are monitored in real-time using a quartz crystal microbalance (QCM).
A cryogenic pump enables the system to reach a base pressure in the 10⁻⁸ Torr range, ensuring high-quality film deposition. Additionally, the chamber is equipped with an ion source, which can be used for substrate cleaning or ion-assisted deposition.

- Available Material: Indium (In)
- Ion Source for Cleaning/Assisted Deposition: Oxygen (O₂) / Argon (Ar)
- Maximum Sample Size: 6 inches
- Substrate Heating: Not available
- Tool Manager: Ida Sadeghi
- Location: Becton 322
- Internal rate: Included with cleanroom access
- User Guide: PDF