Chemical vapor deposition
Yong Sun
DirectorBuilding: Becton Engineering and Applied Science Center, 5th floor
About the instrument
Chemical vapor deposition (CVD) is a method used to deposit films via exposure to volatile precursors. Some common examples are plasma-enhanced CVD, where silane gas is ionized to combine with ammonia to form nitride, or nitrous oxide to form silica. ALD operates through alternating pulses of organometallic precursors and water vapor to form a wide selection of complicated metal oxides. Acceptable materials vary from system to system, so be sure to confirm with a staff member before introducing new substrates to a system. Additionally, be sure you understand the thermal limitations of your substrate.
Available to Yale researchers & external researchers
Equipment
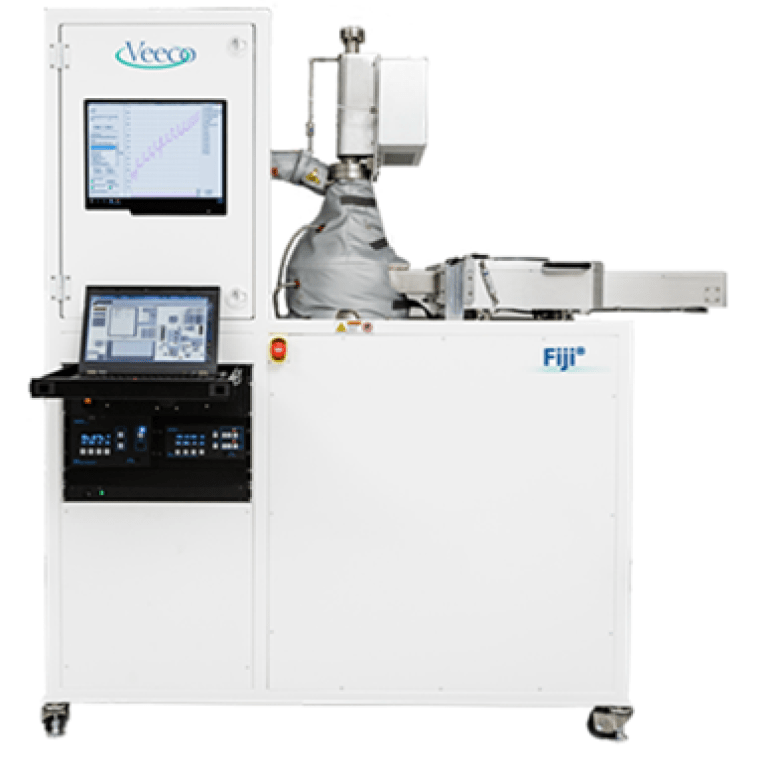
Fiji Plasma ALD
From Veeco’s Product Page: Our Fiji® series is a modular, high-vacuum ALD system that accommodates a wide range of deposition modes using a flexible architecture and multiple configurations of precursors and plasma gases. The result is a next-generation ALD system capable of performing thermal and plasma-enhanced deposition.
- Tool manager: Yong Sun
- Available materials: AlN, AlO, HfO, SiN, SiO, NbN, TiO
- Internal rate: Included with cleanroom access
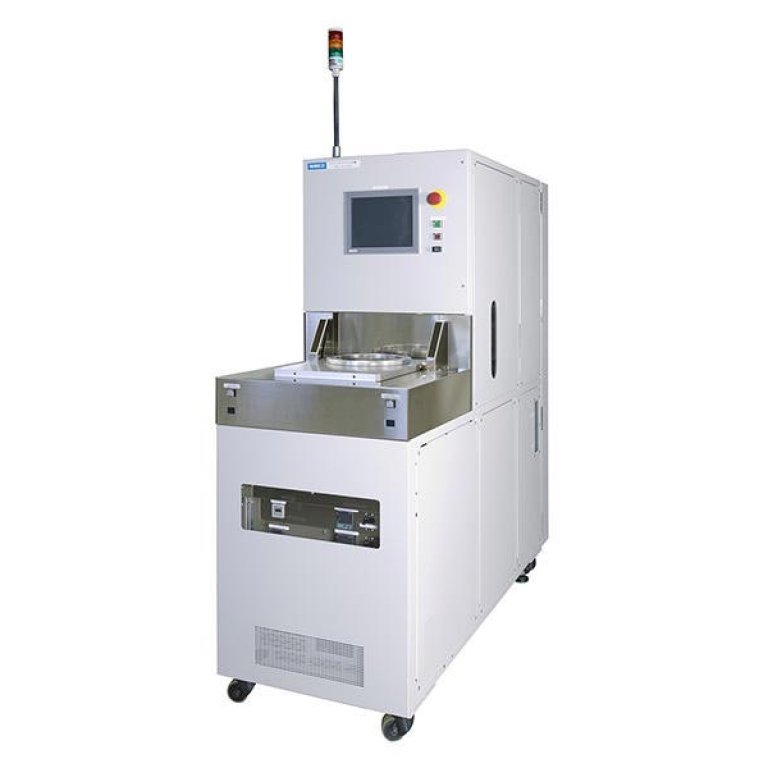
SAMCO PD-220NL PECVD
The SAMCO PD-220NL PECVD uses 5% SiH4, N2O, and NH3 plasma to deposit silicon oxides and nitrides for masking and insulating substrates. The chamber is open-load. Typical process temperatures are 300 to 400 C.
- Tool manager: Yong Sun
- Available materials: SiO2, Si3N4
- Internal rate: Included with cleanroom access
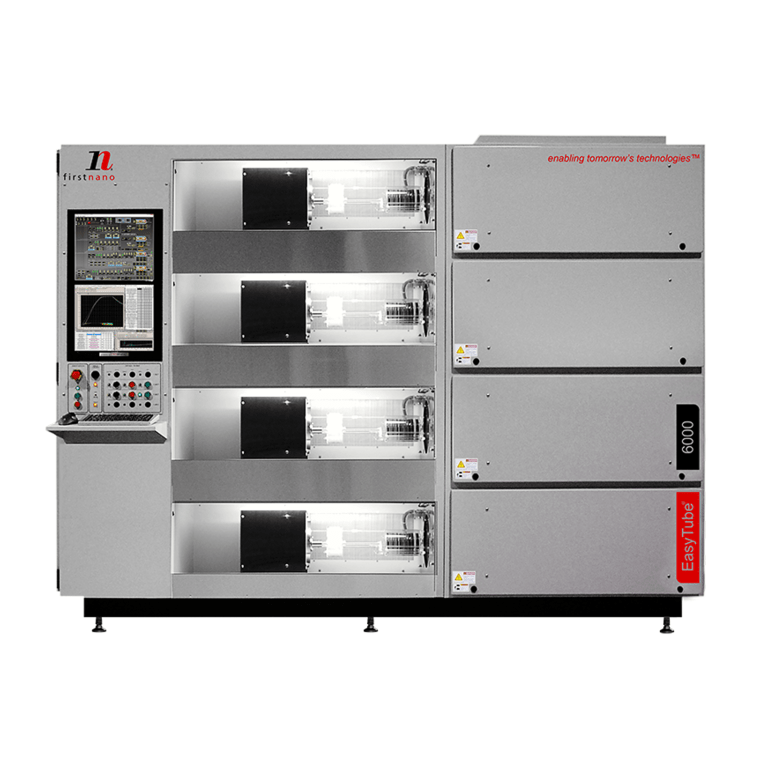
EasyTube Diffusion Furnace
This is a 4-tube diffusion furnace for growing oxides, diffusions, and annealing. Two of the tubes are capable of growing oxides using hydrogen and oxygen to form steam (wet oxidation) or using strictly oxygen (dry oxidation). All tubes are sealed during process and pre-purged with inert gas before admitting process gas. The computer interface allows recipe editing and data logging of the process in each tube. A system control program monitors all vital services to furnace and safety features.
- Tool manager: Yong Sun
- Available gases: H2, O2, N2, Ar, forming gas
- Internal rate: Included with cleanroom access
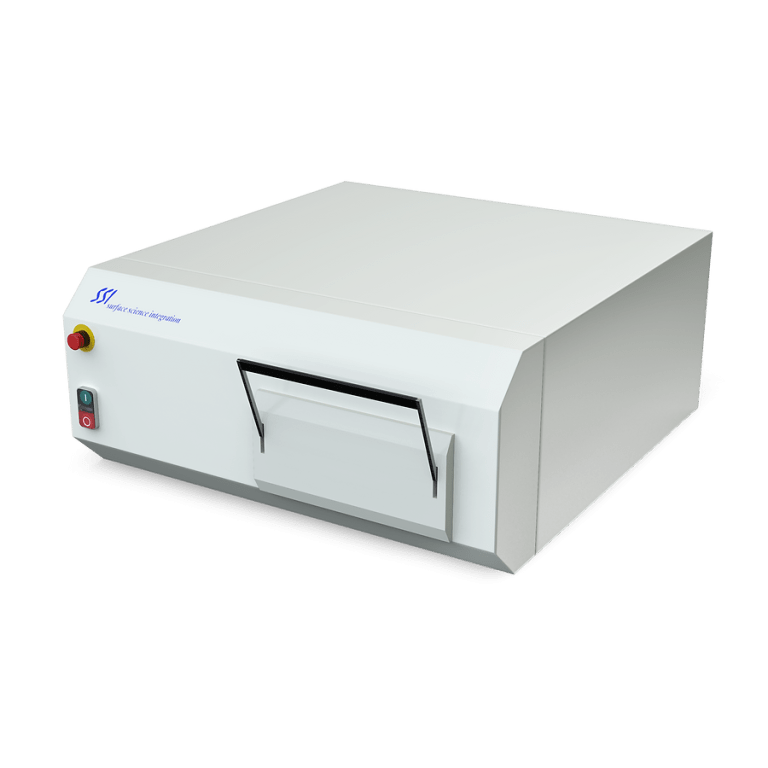
SSI Solaris RTA
The Solaris 150 is a manual loading benchtop RTP system for R&D and pre-production. It can process up to 150mm substrates at a temperature range from RT-1300 degrees. The unique temperature measurement system of the Solaris requires virtually no calibration for different wafer types and backside emissivity differences. The Solaris uses a unique PID process controller that ensures accurate temperature stability and uniformity.
- Tool manager: Yong Sun
- Gases: O2, Ar, N2, N2/H2 (forming gas)
- Wafer sizes: 2”, 3”, 4”, 5” and 6” wafers and pieces
- Ramp-up rate: 10-200°C per second
- Steady-state duration: 0-600 seconds per step
- Ramp-down rate: temperature-dependent, max 150°C per second
- Recommended steady-state temperature range: 200°C - 1250°C
- Thermocouple temperature accuracy: +/- 2.5°C
- Temperature repeatability: +/- 3°C or better at 1150°C wafer-to-wafer
- Temperature uniformity @ 1150°C: +/- 5°C across a 6” (150 mm) wafer
- Internal rate: Included with cleanroom access